Ważnym zagadnieniem we współczesnych technologiach wytwarzania jest poprawa jakości powierzchni technologicznej przedmiotu, mająca na celu zapobieganie pęknięciom i wydłużenie żywotność. Jednym z procesów, który znalazł szerokie zastosowanie w przemyśle jest proces obróbki powierzchni na zimno metodą kulowania (shot peening) śrutem kulistym twardym.
Efekty obróbki zależą od parametrów technologicznych, do których można zaliczyć między innymi: twardość, kształt i wymiary stosowanego śrutu oraz intensywność procesu (energia kinetyczna wyrzucanego śrutu, czas kulowania).
Głównym celem takiej obróbki jest wzmocnienie warstwy wierzchniej elementów narażonych na działanie obciążeń zmiennych oraz na ścieranie. Obróbce tej poddaje się różne przedmioty, jak:
- sprężyny: talerzowe, śrubowe, płaskie, zaworowe, sprzęgłowe,
- osie i wały,
- wały korbowe, korbowody,
- koła zębate,
- stabilizatory,
- łopatki turbin i inne.
Proces kulowania z użyciem śrutu kulistego powoduje powstawanie w warstwie wierzchniej materiału naprężeń ściskających, które bezpośrednio wpływają na trwałość zmęczeniową. W procesie kulowania następuje umocnienie warstwy wierzchniej obrabianego materiału w wyniku odkształceń plastycznych i sprężystych, które przyczyniają się do powstania zmian w strukturze materiału, mikrotwardości i naprężeniach ściskających własnych.
Proces kulowania może być kontrolowany przy zastosowaniu taśmowego testu Pasek Almen, który wskazuje energię wywieraną przez uderzenie śrutem. Pasek wykonany jest ze stali sprężynowej o określonej twardości i płaskości, jest poddawany działaniu śrutu z jednej strony, co powoduje jego wyginanie albo zakrzywienie. Stopień zakrzywienia jest proporcjonalny do energii (prędkości i masy śrutu) przekazanej przez uderzenie i jest mierzalny na mierniku Almen.
Dynamiczny proces kulowania realizowany jest w kulownicach wirnikowych KW produkcji IdeaPro. W Kulownicach śrut kulisty wyrzucany jest przez wirniki rzutowe z prędkością 40÷80 m/s i uderza w obrabianą powierzchnię, wywołując trwałe plastyczne odkształcenia na powierzchni obrabianego przedmiotu.
Kulownice wirnikowe typu KW produkowane przez IdeaPro są dostosowane do procesu technologicznego wymaganego przez klienta w zakresie: zastosowanego materiału, kształtu i wielkości obrabianego przedmiotu oraz wymaganej wydajności. Przy wyborze odpowiedniego rodzaju urządzenia do kulowania brana jest również pod uwagę jego lokalizacja u klienta.
Budowa i działanie kulownic wirnikowych typu KW wzorowana jest na oczyszczarkach wirnikowych, które są w ofercie produkcyjnej IdeaPro w Nowej Soli. Podstawowymi zespołami kulownic wirnikowych typu KW są wirniki rzutowe wyrzucające śrut z dużą energią na powierzchnię obrabianego przedmiotów. Obieg śrutu w kulownicach jest w układzie zamkniętym. Śrut podawany do wirników rzutowych wyrzucany jest z dużą energią na powierzchnię obrabianego przedmiotu, następnie poprzez perforowaną podłogę opada grawitacyjnie do zsypu, skąd przenośnikiem śrubowym i dalej przenośnikiem kubełkowym transportowany jest do układu separacji powietrznej lub powietrzno-magnetycznej, w celu jego oczyszczenia z zanieczyszczeń. Tak oczyszczony śrut z seperatora przesypuje się do zbiornika, z którego przez dozowniki śrutu podawany jest ponownie do wirników rzutowych.
Kulowanie przedmioty wymagają różnego stopnia utwardzenia powierzchni. Realizowane jest to przez zmianę czasu ich przebywania w strugach wyrzucanego przez wirniki rzutowe śrutu. Zastosowanie przemienników częstotliwości do regulacji obrotów silników wirników rzutowych umożliwia regulację energii kinetycznej wyrzucanego śrutu, a tym samym dynamiki procesu kulowania.
Kulownice mogą pracować w cyklu automatycznym oraz remontowym. Sterowanie pracą urządzenia realizowane jest za pomocą elektronicznego systemu sterowania PLC. Kulownica wyposażona jest w system blokad i zabezpieczeń gwarantujących bezpieczeństwo pracy obsługi oraz uniemożliwiających uszkodzenia mechanizmów. Aby zapewnić bezpyłową pracę kulownic zastosowane są układy odpylania z wentylatorem, który wytwarza wymagane podciśnienie wewnątrz komory kulownicy. Układ odpylania przeznaczony jest do oczyszczenia zasysanego powietrza z kulownicy. Filtry mogą być wyposażone w worki filtracyjne lub wkłady patronowe. Obydwa systemy odpylania posiadają powietrzną regenerację worków filtracyjnych lub wkładów.
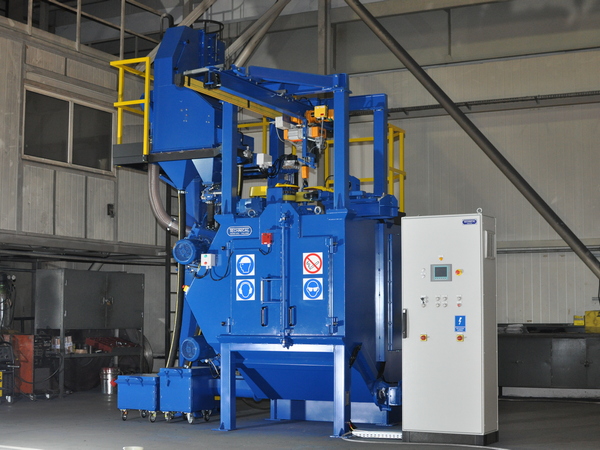
Kulownica do kół zębatych
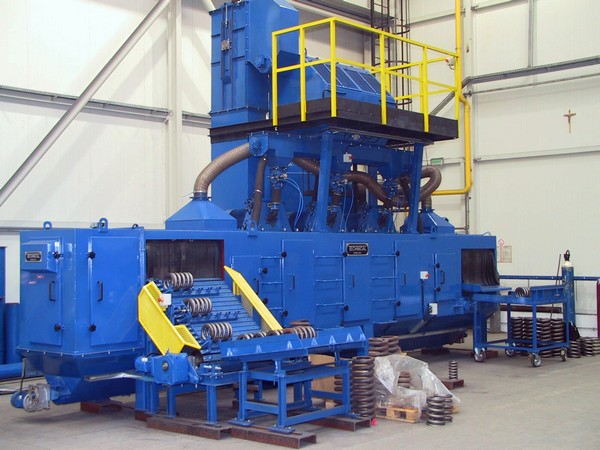
Kulownica do sprężyn
Specjaliści IdeaPro, posiadający wieloletnie doświadczenie w projektowaniu, produkcji oraz eksploatacji kulownic wirnikowych, służą pomocą w doborze odpowiedniego urządzenia zgodnego z wymaganiami klienta co do wielkości i wydajności.
W wielu przypadkach pomoc naszych specjalistów jest nieodzowna szczególnie w:
- pomocy w usytuowaniu, lokalizacji kulownicy w istniejących obiektach,
- wykonaniu założeń branżowych, jak: instalacje elektryczne, sprężonego powietrza lub odpowiednich projektów, np. wymaganych do pozwolenia na budowę,
- wykonanie założeń fundamentowych lub projektu fundamentów,
- doborze odpowiedniego system odpylania dostosowanego do warunków pracy kulownicy,
- optymalizacji jakości procesu kulowania oraz wydajności,
- pomocy w pozyskaniu środków z UE oraz innych programów.
Wszelkie bardziej szczegółowe pytania prosimy kierować bezpośrednio do IdeaPro.
Nasz doświadczony zespół specjalistów chętnie udzieli Państwu wszelkich informacji i pomocy.